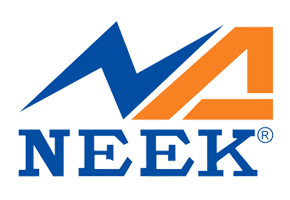
Description
NEEK was established in a joint venture between young Nepalese Entrepreneurs and “Ekarat Engineering Public Co. Ltd:’ of Thailand in the year 1990. With continued support from our valued customers over the years, we have been able to serve for the last twenty-five years in the manufacturing and supply of Distribution Transformers.
NEEK has a capacity to manufacture up to 10 MVA and up to 132 kV class Distribution Transformers. The manufacturing plant at Hetauda is equipped with state-of-art equipment and a highly skilled technical work force. From 1992, we have manufactured various ratings of distribution transformers and supplied to the electricity utilities, hydropower projects, small hydro powers, hospitals, shopping complex and industries. We have also completed the successful repair and maintenance work of Power Transformers up to 10MVA 3-Phase, 33/11 kV and Power Transformers up to 30 MVA 3-Phase, 132/11 kV. This gives us the extra insight while manufacturing our product, for our customers.
The first product of NEEK was launched in August 1992 and with that, NEEK has been consistent in quality and continues to make the most sought after transformers in the country. Out of the installed Distribution Transformers in Nepal, most of the quantities have been supplied by NEEK. The total production capacity and its product range makes NEEK the largest and the most efficient manufacturer of Distribution Transformers in the country.
To keep pace with the changing technology and upgrades, regular training is provided to NEEK employees at all levels. Our refresher programs allow workers to benefit from local or foreign experts and our Engineers are sent abroad for training in related fields to be updated with present technological upgrades.
Nepal Ekarat Engineering has been exclusive in being able to offer products manufactured according to customer requirements in a clean, healthy and safe environment. All incoming raw materials are carefully chosen, inspected and tested before it is used for these long-life products. From core laying, coil winding, tank fabrication and assembly, each step is carefully monitored by experts and tested by the latest equipment for the quality and in accordance with the international standards.
NEEK is certified with the ISO 9001: 2015, as an adherence in the manufacturing of quality products in a clean, healthy and safe environment that follows the principle and procedures of QMS in every aspect of our manufacturing process for the continual improvements of quality in our products. We have recently achieved the NS Standard for our transformers.
45 kWh Electricity
3400
Transformer from 1 KVA – 10000 KVA rating
Supplier Video
Iron Core
Cold Rolled Grain Oriented (CRGO) magnetic silicon steel sheets of high quality are used to make the iron core. The most practical transfer of magnetic flux from the limbs to the yoke is achieved by inter-leaving the alternate joints, thus reducing no load losses.
HV and LV Winding
Round enamel-insulated copper conductors are wound to form layer type, disc type-high voltage coils. The coils are wound with constant tension directly onto a pressboard cylinder. The layer insulation papers adapted according to electrical requirements. Paper-insulated rectangular copper conductors are used to form wound layer type low-voltage coils, wound with constant tension directly onto a pressboard cylinder. Ample measures are taken to ensure the mechanical rigidity and the electrical soundness of both the HV and LVcoils
Corrugated Plate
The tank and cover are made of high quality sheet steel, which has to pass a stringent quality test. The tank is fabricated on a rigid bottom with an oil drainage outlet, corrugated sidewalls and a upper frame. After the components are welded together, the first leakage test is performed on the tank. Internal surfaces are prepared for painting by sand blasting. The standard paint finish is a two-coast process of rust inhibiting primer followed by a high specification finish coating. The tank provides structural strength to the complete product and the design has the main influence on heat dissipation
Bushings
HT bushings shall have full wave impulse withstand voltage or basic impulse insulation level (BIL) as per the IEC Standard / DIN Standard / IS Standard.
Tap - Changer
In order to provide a constant output voltage despite of the voltage fluctuation on the input system the high voltage windings are provided with the tapings connected to an off-circuit tap-changer mounted on the tank cover and operated externally. The tapping positions are fixed by means of locking pins. On-load tap changer can be upon request and also the tapping position for the off-circuit tap changer can be adjusted upon customer’s requirement.
Vacuum Drying
The core-cost assembly and tanks are placed in a vacuum oven chamber to extract the accumulated moisture. Immediately after drying, the transformers are tanked and filled with pre-dried, degassed transformer oil. The required quality of the oil is confirmed by the laboratory tests.
BUCHHOLZ RELAY
This protects the transformer from damage due to internal short circuits and faults. The alarm contact in the double float design signals oil sinkage and formation of gas, while a trip contact is activated in the event of server malfunctions. This can be available upon customer request for a lower rating Distribution Transformers below 1500 kva also
Dial Thermometer
It shows the actual oil temperature. Alarm and Signals are provided as protection against overloading.
Transformer Oil
Each Transformer shall be supplied with high quality, clean, dry and tested oil, which complies with the BS 148/84, IEC 296 standards.
TRANSFORMER PURCHASE ON A TOTAL OWING BASIS